Auto elettriche: due rivoluzioni silenziose, dove Tesla è già in pole position
Le batterie LFP con catodi ferro e fosforo, nonché la pressofusione di stampi con una nuova lega sono la nuova frontiera dell'automotive
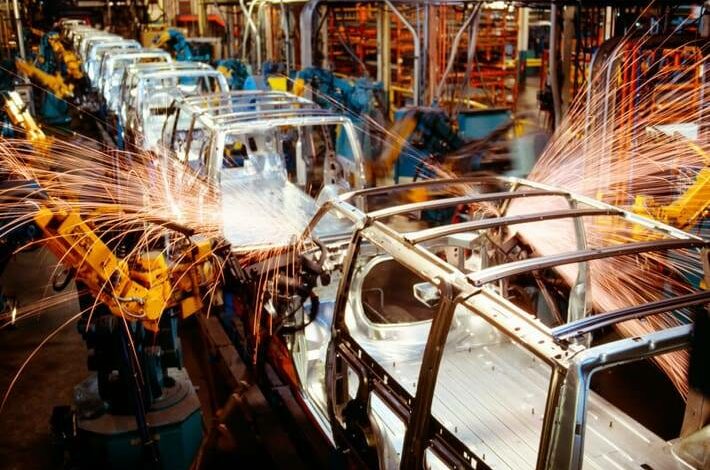
L’industria dei veicoli, soprattutto elettrici, è senza dubbio a una svolta epocale grazie ad almeno due novità tecnologiche poco reclamizzate, ma note agli addetti ai lavori. La prima riguarda la transizione dalle batterie agli ioni di litio con catodi NMC (nichel, manganese e cobalto) ai modelli con catodi LFP (ferro e fosforo). La seconda riguarda l’adozione del Giga-casting, ovvero grandi stampi di pressofusione che riducono a pochi parti il numero di elementi per comporre un’auto – la tecnica è già impiegata da Tesla per la Model Y.
Dalle batterie Ioni di Litio NMC alle LFP
Le batterie agli Ioni di Litio NMC normalmente presenti sul mercato hanno una densità di energia di circa 270 Wh/kg, che consente a un veicolo elettrico di viaggiare nella migliore delle ipotesi fino a 450 km o poco più. Il problema è che il nichel e il cobalto provengono rispettivamente da Russia e Congo: il primo ormai oggetto di sanzioni e il secondo con pratiche di lavoro discutibili. Senza contare il fatto che il cobalto, quotato a fine 2017 circa 32mila dollari a tonnellata, la scorsa primavera ha raggiunto gli 82mila dollari per poi stabilizzarsi sulla soglia dei 50-55mila.
Poi c’è il problema dell’instabilità termica e dei 1000 cicli massimi operativi che dovrebbero assicurare teoricamente 10 anni. I modelli ferro e fosforo fino ad ora soffrivano di qualche limite, come ad esempio una densità di energia inferiore che si rifletteva sul peso complessivo e prestazioni ridotte nella fase di carica con temperature basse. Ora però qualcosa è cambiato grazie a nuovi accorgimenti. Gli esperti concordano sul fatto che le soluzioni LFP forniscono quasi cinque volte più cicli di carica delle NMC, hanno velocità di carica/scarica più veloce, sopportano meglio la ricarica rapida, gestiscono meglio la guida ad alte prestazioni e soprattutto è facile reperire i loro componenti.
Il tema centrale rimane comunque il presunto divario di densità energetica. Secondo Dan Blondal, CEO dell’azienda di batterie Nano One, la differenza di densità di energia esiste a livello di singola cella ma la ridotta instabilità termica consente un allestimento basato su forma prismatica invece che cilindrica. In sintesi si può ridurre il peso della batteria, anche grazie alla tecnologia cell-to-frame (o cell-to-pack), che trasforma la cella in parte della struttura del pacco batteria.
“Con una densità di energia di 250 Wh/kg nel nostro formato prismatico VLF proprietario, la densità di energia del nostro Advanced LFP è dal 30% al 50% superiore rispetto ad altre celle LFP disponibili in commercio, che si traduce in un aumento equivalente dell’autonomia del veicolo. E poiché la produzione di celle LFP avanzate non costa di più, questa nuova linea non costa di più. I veicoli che usano già LFP e dispongono di un’autonomia sufficiente, con il passaggio a Advanced LFP assicureranno alle case automobilistiche un impiego minore di celle, e un conseguente risparmio per i consumatori“, ha dichiarato Tim Poor, presidente di Advanced Cell Engineering a engineering.com. Non a caso Tesla impiega già batterie LFP, almeno su alcuni modelli. In un rapporto pubblicato ad agosto UBS ha stimato che LFP conquisterà il 40% del mercato delle batterie entro il 2030, praticamente un aumento del 25% rispetto alle previsioni precedenti. In sintesi hanno dalla loro costi più bassi, prestazioni adeguate e un minor impatto ambientale.
Pressofusione, ma in grandi dimensioni
La pressofusione è una tecnica che prevede l’iniezione di metallo fuso ad alta pressione in uno stampo metallico. Non è una novità nel settore industriale – risale al 1800 – ma in campo automobilistico oggi è impiegata per realizzare molti componenti invece che pochi di grandi dimensioni. In pratica si realizzano centinaia di parti pressofuse, come ad esempio i cilindri del motore, staffe e altri elementi, che vengono poi assemblate su una catena di montaggio automatizzata. Il cosiddetto Giga-casting invece consente ad esempio a Tesla di produrre più agevolmente le Model Y perché viene eseguita la fusione di due o tre pezzi di grandi dimensioni. Si riducono i costi e la complessità del processo produttivo.
“Per ottenere auto elettriche a prezzi accessibili con una buona autonomia, ha dovuto rendere accessibili le strutture in alluminio“, ha spiegato Gregory Olson, docente del MIT, parlando di Elon Musk. “Così ha esaminato il tipo di pressofusione per i modellini di auto e ha detto: ‘Perché non ingrandirlo? Ci faremo l’intera macchina‘”. L’azienda, come Apple per il Watch, si è affidata all’approccio computazionale di Olson che sfrutta la modellazione e la simulazione al computer per comprendere e progettare nuovi materiali. Il problema è che con l’aumentare delle dimensioni il trasferimento di calore è più lento e i tempi di ciclo diventano così lunghi da rendere l’operazione meno efficiente ed economicamente vantaggiosa.
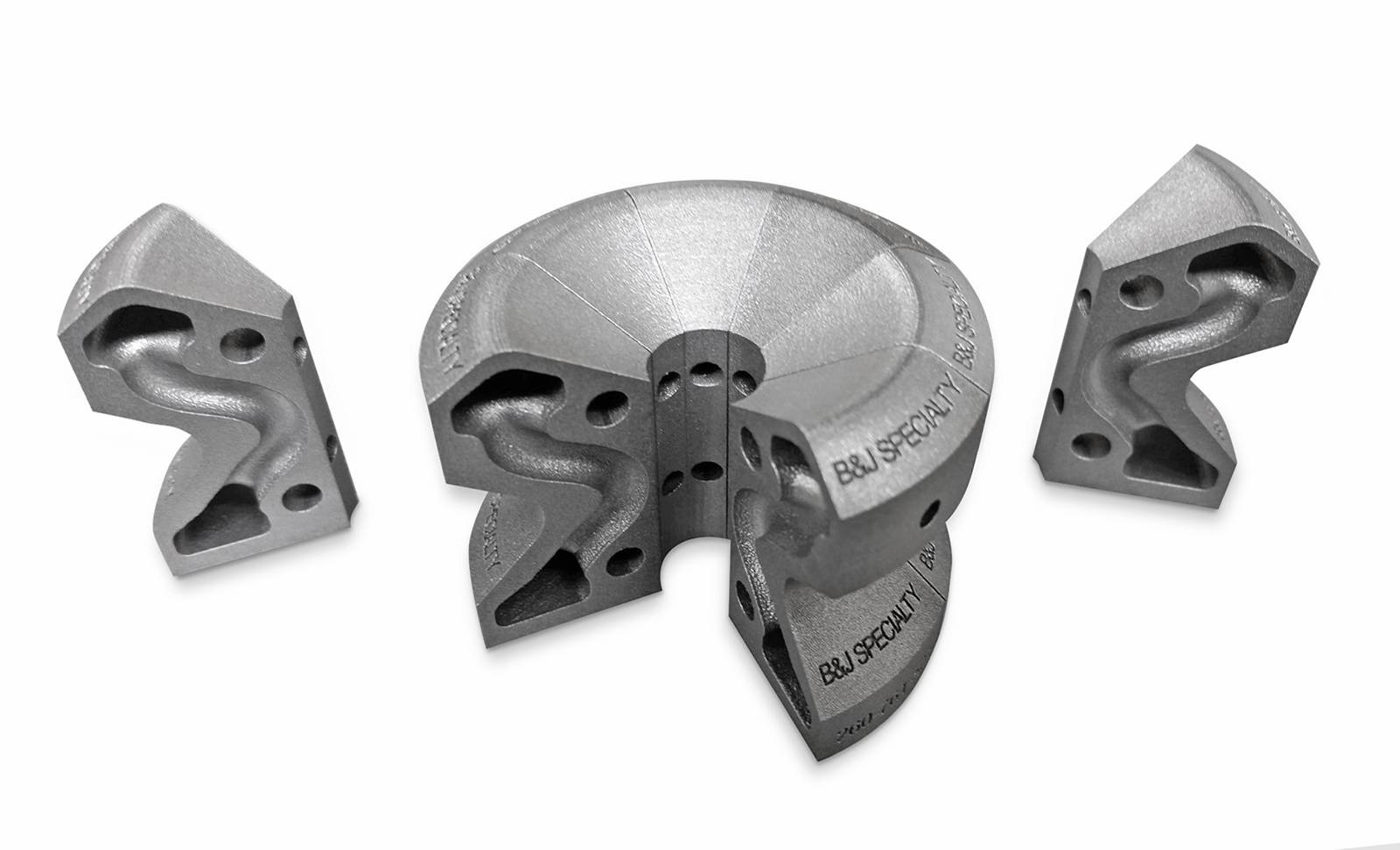
La soluzione? Una tecnica chiamata raffreddamento conforme che prevede canali stretti lungo l’oggetto da realizzare per far scorrere acqua o refrigerante e quindi accelerare il processo di raffreddamento. Ed è qui che si è manifestata recentemente un’altra novità: i giovani ricercatori Ian Chen e Kyle Markland del MIT hanno sviluppato una lega di acciaio stampabile in 3D (produzione additiva) ideale per realizzare gli stampi di grandi dimensioni per l’automotive, e non solo. Perché come ha sostenuto Olsen gli acciai convenzionali “sono piuttosto fragili e soggetti a rotture se si tenta di stamparli“.
E così si è giunti a una nuova lega metallica, inizialmente fusa e poi nebulizzata in minuscole goccioline che si solidificano, formando una polvere. Dopodiché la polvere viene stratificata e fusa dal laser in un oggetto in una stampante 3D. “Abbiamo progettato un acciaio per utensili molto promettente, con prestazioni superiori in termini di conducibilità termica, durezza e tenacità, che può essere effettivamente stampato“, ha assicurato Florian Hengsbach, anche lui ricercatore ma dell’Università di Paderborn, in visita al MIT.
Il team ha depositato la domanda di brevetto negli Stati Uniti e sono già state attivate trattative con Tesla. Ed ecco spiegato il motivo per cui il 9 settembre scorso Musk ha twittato: “Prendi Scienza dei Materiali 101. Non te ne pentirai“. Appunto il corso base universitario di scienza dei materiali.